Oh, great: Rat populations are surging as cities heat up
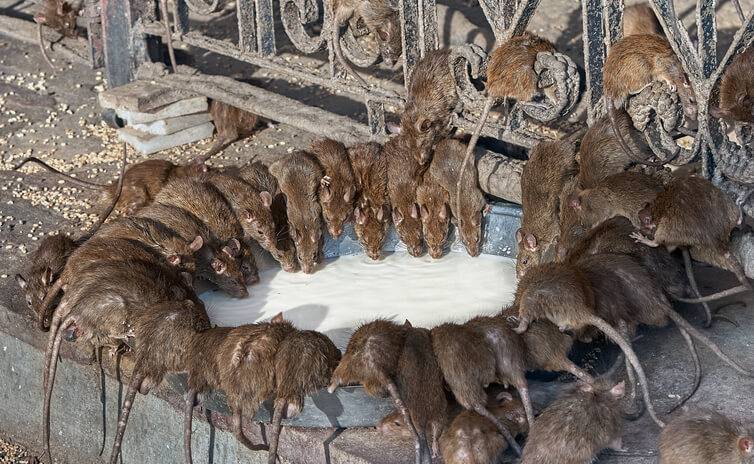
Rats are in many ways better adapted to cities than the humans that built them. While urbanites struggle with crowds, sparse parking spaces, and their upstairs neighbors stomping around at 4 a.m., rats are living their best lives. Huddled safely underground, they pop up at night to chew through heaps of food waste in dumpsters and hot dogs left on stoops.
Now scientists have found yet another gnawing advantage for rats. A study published on Friday in the journal Science Advances found that as temperatures climb in cities, rat populations are growing, even as city dwellers suffer. “In cities that have experienced the fastest warming temperatures, they tended to have faster increases in their rat numbers as well,” said Jonathan Richardson, an urban ecologist at the University of Richmond and lead author of the paper. “Females will reach sexual …